How to Properly Install Carbon Steel Fittings for Maximum Efficiency
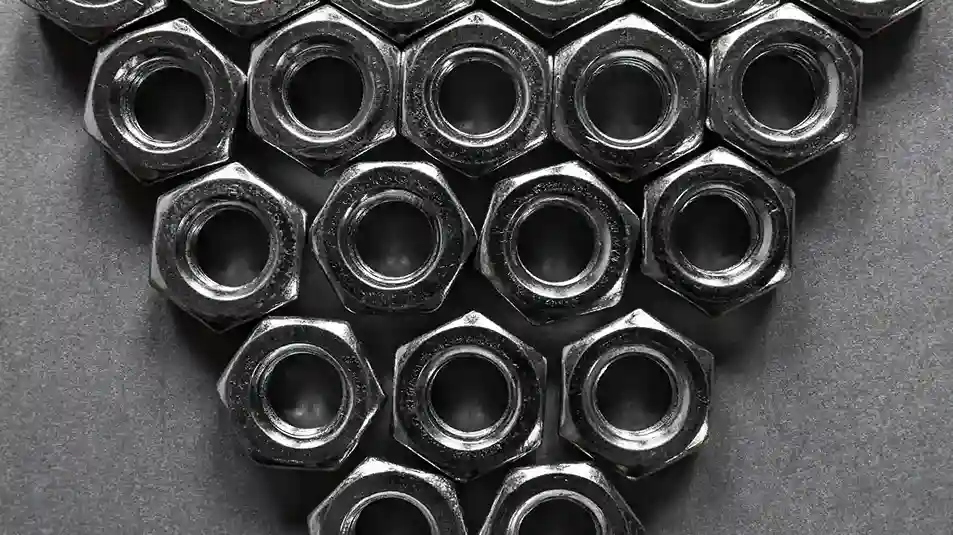
When it comes to the construction and maintenance of industrial systems, proper installation of carbon steel fittings is critical for ensuring maximum efficiency, durability, and safety. As a carbon steel fittings supplier in Qatar, NWH Qatar understands the importance of quality installation practices and their role in the smooth operation of pipes, valves, and other critical components in various industries. Whether you’re working on an oil and gas project, an industrial plant, or a commercial facility, proper installation of carbon steel fittings will prevent costly repairs, improve system performance, and extend the life of your equipment.
Understanding Carbon Steel Fittings
Before diving into the installation process, it’s important to understand the role of carbon steel fittings in a piping system. These fittings, made from carbon steel, are essential for connecting, redirecting, or controlling the flow of fluids and gases through pipes. They come in various shapes, sizes, and designs, including elbows, tees, reducers, and couplings, among others.
Carbon steel is a popular material due to its high strength, durability, and affordability. However, it is susceptible to corrosion if not properly installed and maintained, making correct installation essential for ensuring maximum efficiency.
Steps to Properly Install
1. Choose the Right Fittings for the Job
Selecting the right carbon steel fittings for your project is the first and most important step toward ensuring an efficient installation. This involves considering the type of fluid or gas being transported, the pressure and temperature requirements, and the pipe size. For example, if you are working on a high-pressure system, you’ll need fittings rated for such conditions. As a pipe supplier in Qatar, NWH ensures that customers have access to the right products suited to their specific project needs.
Using the correct fittings will help avoid leakages, flow restrictions, and premature wear, ensuring long-term efficiency. Always check the specifications for the fittings before installation to verify their compatibility with the existing system.
2. Prepare the Pipes and Fittings
Once you’ve selected the right fittings, it’s crucial to properly prepare both the pipes and the fittings before beginning the installation. Ensure that the pipe ends are cut cleanly and squarely, with no burrs or sharp edges. This will help create a tight seal and reduce the risk of leakage. Use a pipe reamer or a deburring tool to smooth any rough edges left from the cutting process.
For carbon steel fittings, inspect each piece for signs of defects such as cracks or deformations. If any issues are found, replace the damaged fittings immediately to avoid future system failures.
3. Use Proper Sealants and Thread Compounds
When installing threaded carbon steel fittings, it’s essential to apply the correct thread sealant or compound to prevent leaks. Teflon tape or pipe joint compound is commonly used for this purpose. Be sure to use a sealant that is compatible with both the pipe material and the fluid or gas being transported.
For welding applications, the need for sealants is eliminated, as the welding process itself provides a strong, leak-proof connection. However, proper welding techniques must be followed to avoid compromising the integrity of the fitting and pipe connection.
4. Properly Align the Fittings
Before securing the fittings to the pipes, make sure they are aligned correctly. Improper alignment can lead to stress on the system and cause fittings to break or leak over time. Using pipe supports and hangers can help align the pipes and reduce the strain on the fittings.
In addition to ensuring proper alignment, make sure the fittings are positioned in such a way that they can be easily accessed for future maintenance or repairs. This may require some planning and foresight, particularly in large or complex systems.
5. Tighten the Fittings Securely
After aligning the fittings and ensuring that all threads are sealed properly, it’s time to tighten the connections. When tightening threaded fittings, use the appropriate tools to ensure a firm and secure fit without over-tightening, which can cause damage to the threads or fittings.
For flanged or welded fittings, use a torque wrench to tighten the bolts to the specified torque value. This helps to distribute the pressure evenly across the fitting, preventing leaks and ensuring the connection remains strong under operational conditions.
6. Perform Leak Tests
After completing the installation, it is essential to test the system for leaks. This step ensures that all connections are secure and that no pressure is lost in the system. A common method of leak testing involves pressurizing the system with air or water and inspecting the fittings for any signs of leakage.
If a leak is detected, shut down the system immediately and identify the source of the issue. This may involve re-tightening the fittings, applying more sealant, or replacing damaged components. A thorough leak test is essential to ensure that the system will operate at full efficiency once it is in service.
7. Regular Maintenance and Inspections
Once the carbon steel fittings are installed and the system is operational, ongoing maintenance is essential for keeping the system running efficiently. Look for any signs of leaks, and be proactive in addressing any issues before they escalate.
Regular inspections and maintenance can help extend the life of the carbon steel fittings and ensure that the system continues to operate at peak performance. Always consult with an experienced professional when performing maintenance or if any concerns arise.
Why Quality Installation Matters
Proper installation of carbon steel fittings directly impacts the performance and longevity of the system. When fittings are incorrectly installed, it can lead to leaks, reduced flow efficiency, and system downtime. This not only results in higher operational costs but also poses safety risks, particularly in high-pressure or hazardous systems.
As a carbon steel fittings supplier, NWH Qatar emphasizes the importance of using high-quality materials, and professional installation practices to ensure that your piping system operates smoothly and efficiently for years to come.